
Digital Manufacturing for an Intelligent Enterprise


The new technological advances in complex algorithms, data processing and storage has made the Fully Automated Fulfillment centers a reality where a large number of Robots work in tandem to fulfill customer demands for ‘Make to Stock(MTS)’ products. We see several such use cases and production deployment of Robots for demand fulfillment with increased fulfillment throughput.
While the organizations are re-orienting their business processes to be more customer-centric, the next level of technological advances will re-design the 'Make to Order(MTO)'or 'Engineered to Order' manufacturing and fulfillment processes. The concept of ‘Mass customization’ is evolving and manufacturers are experimenting with the different aspects of the same. This article will try to share a perspective on next generation MES (Manufacturing Execution Systems) relevant to Industry 4.0.
Mass Customization on the Production
Mass customization on the production line is being attempted by organizations which have been able to integrate all the ends of the fulfillment processes to an enterprise wide platform with seamless information exchange. The SCOR v12 model defines Agility as one of the five attributes for performance benchmarking of a supply chain process and Agility in customer order fulfilment is an important aspect. There are organizations which have matured the processes of offering ‘customized product’ on their customer facing(CRM) applications, where a customer can request his/her own configuration of a product available from the catalogue and this unique demand is then fulfilled. These are then integrated to the organization’s Supply Chain Operations Systems (ERP) for demand & supply planning; to fulfill the customer’s order in the shortest possible time & lower cost. Still, we have manufacturing process, which is decoupled from individual demands and this reduces the Order Fulfillment Rate(OFR) and ultimately impacts the customer experience. iMES (Intelligent Manufacturing Execution System) which is able to drive the agility in the production process will help in this by creating bridge between various shop floor systems and providing seamless integrated ecosystem for real-time information visibility for better and faster decision making.
This Smart system will have the capability to integrate with a variety of applications /protocols. On one end,it is integrated to the ERP to translate the production schedule plan from MRP system to the assembly line for production run; and on the other hand, it is able to capture the IIoT data pushed by the machines on the shop floor. Let us discuss these in details:
Production plan Translation to Actual Production Run:The system is designed to accept the MRP & production schedule data on the production BOM, it is getting the real-time update on the line throughput, work center’s health, WIP/sub-assembly inventory and other shop floor data. The data ingestion platform is able to accept variety of M2M, PLC/CNC, SCADA data transmission modes through device gateway which is connected to the Cloud for storing the same in Data Lakes. The application layer of the cloud - the iMES ‘Engine,’ which will be able to drive the Production scheduling, work center reconfiguration as per the instance of the product(color, variants, and others); monitor the shop floor & report on real-time basis. iMES will also have the simulation capabilities for the next Production Schedule and will provide the demand fulfillment scenarios. Think of a situation where delaying a specific batch of order brings cost saving in the manufacturing process; if small delay to customer is acceptable or we are able to offer better product variant or better deal. Based on the actual output, the back feed will go to the MRP system for corrections in the next Production Schedule run as necessary. The system will also have logic to propose the best product variant based on the WC’s configuration and sub-assembly inventory lying idle for typical MTS scenario. The complexity increases as the mix of MTO & MTS becomes the production schedule scenario. The iMES will also be able to suggest to delay or pre-pone the Customer Order Decoupling Point (CODP) as per the production plan.
"While the organizations are re-orienting their business processes to be more customer-centric, the next level of technological advances will re-design the ‘Make to Order (MTO)’ or ‘Engineered to Order’ manufacturing and fulfillment processes"
Asset Tracking & Data Exchange: The IIoT-enabled machines will be pushing a lot of information on the run parameters, output conditions, and the state of machines. The platform will be able to utilize the AI & ML APIs to predict the state of the machines for the near future and accordingly propose actions. Parking of a truck in the unloading bay will initiate the unloading bins/pallets trolley to align to an inbound load. These are the use cases for what we call ‘self-orchestrated’ shop floor with minimal/no human intervention Data exchange through common standards to Supply chain partners is also an important aspect as this will enable decision making with a holistic data.
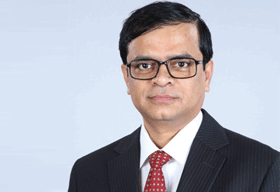
Sandeep Kulkarni
Data Analytics & Intuitive Dashboards: The machine level details of the shop floor is available for the Plant Supervisor to take decisions regarding plant operations, reliability centered maintenance and health of the capital intensive machines. A hierarchical view of the organization can be represented and data from manufacturing line, transactional ERPs, PLCs, assembly line applications, QM results, and so on is aggregated in Data Lakes. The system will be capable of mapping capacity utilization insights, machine idle time and defect rates in a hierarchical structure as per organization view or these can be switched to a product view by click of a mouse. Aggregate, as well as the granular view of the Supply Chain elements will increase the transparency across the elements, resulting in net higher cash availability for the organization. The bottoms-up approach of decision-making or investment decision will be facilitated by the time series data view from supply chain elements and associated variance analysis.
With modern technological tools like IoT, RPA and big data analytics at our disposal, organizations can be better equipped in addressing ever changing customer expectations by brining agility in the supply chain coupled with real time visibility across entire value chain. Also it will help in creating and enhancing new delivery models and better customer experience. iMES along with four pillars of manufacturing – production management, inventory management, quality management and maintenance management can really help create MES driven smart factory.
"While the organizations are re-orienting their business processes to be more customer-centric, the next level of technological advances will re-design the ‘Make to Order (MTO)’ or ‘Engineered to Order’ manufacturing and fulfillment processes"
Asset Tracking & Data Exchange: The IIoT-enabled machines will be pushing a lot of information on the run parameters, output conditions, and the state of machines. The platform will be able to utilize the AI & ML APIs to predict the state of the machines for the near future and accordingly propose actions. Parking of a truck in the unloading bay will initiate the unloading bins/pallets trolley to align to an inbound load. These are the use cases for what we call ‘self-orchestrated’ shop floor with minimal/no human intervention Data exchange through common standards to Supply chain partners is also an important aspect as this will enable decision making with a holistic data.
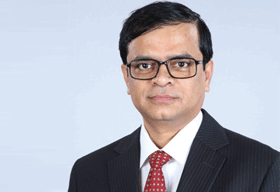
Sandeep Kulkarni
Data Analytics & Intuitive Dashboards: The machine level details of the shop floor is available for the Plant Supervisor to take decisions regarding plant operations, reliability centered maintenance and health of the capital intensive machines. A hierarchical view of the organization can be represented and data from manufacturing line, transactional ERPs, PLCs, assembly line applications, QM results, and so on is aggregated in Data Lakes. The system will be capable of mapping capacity utilization insights, machine idle time and defect rates in a hierarchical structure as per organization view or these can be switched to a product view by click of a mouse. Aggregate, as well as the granular view of the Supply Chain elements will increase the transparency across the elements, resulting in net higher cash availability for the organization. The bottoms-up approach of decision-making or investment decision will be facilitated by the time series data view from supply chain elements and associated variance analysis.
With modern technological tools like IoT, RPA and big data analytics at our disposal, organizations can be better equipped in addressing ever changing customer expectations by brining agility in the supply chain coupled with real time visibility across entire value chain. Also it will help in creating and enhancing new delivery models and better customer experience. iMES along with four pillars of manufacturing – production management, inventory management, quality management and maintenance management can really help create MES driven smart factory.